Metal objects are ubiquitous in our daily lives, from the aluminum shells of laptops to the bodies of cars, the metal frames of smartphones.
But do you know how these metal parts or products are made?
Before being mass-produced, designers will first use Rapid Metal Prototyping methods to create physical models of their designed metal parts or products in order to validate their ideas or get user feedback.
This blog will help you get a detailed understanding of Rapid Metal Prototyping, including methods, materials, finishing, and costs.
What is Rapid Metal Prototyping?

Rapid Metal Prototyping is the process of creating early versions of products or models using metal as the base material through rapid production methods. This technology allows engineers and designers to quickly realize and test new ideas, thereby accelerating the entire product development cycle from concept to market.
Rapid Metal Prototyping Methods
There are many manufacturing methods for Rapid Metal Prototyping, each with its own advantages.
Today, let’s explore 5 Rapid Metal Prototyping Methods:
Metal CNC Machining
CNC machining is a method of automated manufacturing that uses computer programs to direct the actions of machine tools. This process involves cutting away layers of material to produce custom parts. CNC machining is flexible, Can be used with materials such as metals, plastics, wood, glass, foam and composites.
Advantages of CNC machining
- High Precision: CNC machining can achieve extremely high dimensional accuracy, typically between 0.005-0.01mm and is not affected by the complexity of the part.
- High Automation: CNC machine tools reduce manual operation, improve production efficiency, and can be integrated into unmanned factories through automatic loading and unloading systems.
- Strong Adaptability: When changing the machining object, only reprogramming is required without other complex adjustments, shortening the production preparation cycle.
- Complex Part Machining: CNC machining can produce parts with complex shapes that cannot be completed by manual machining.
- Repeatability: CNC machined parts are highly precise and repeatable, making them suitable for mass production.
CNC Manufacturing Methods
There are many types of CNC machines used for Metal Prototyping, each one specializes in manufacturing metal parts with different structures. Let’s see 3 CNC machines:

CNC TURNING
CNC truning is primarily used for creating symmetrical parts with external contours, it is ideal for producing components like axles, bearings, and bushings.

CNC MILLING
CNC milling can produce complex geometries, flat surfaces, slots, pockets, and contours on various materials include both plastic and metal materials.

CNC DRILLING
CNC drilling is a specific type of machining that focuses on hole creation, from simple through-holes to complex multi-level holes and deep drilling operations.
Metal 3D Printing
3D printing is an additive manufacturing process that builds objects by adding material layer by layer, based on a 3D model, unlike traditional subtractive manufacturing like CNC where material is removed from a block.
Advantages of 3D Printing
- Design Flexibility: 3D printing can create complex geometries that may be difficult or too costly to produce with traditional methods.
- Customization: Easy to modify designs for personalized customization, ideal for small batch production and custom products.
- Rapid Prototyping: Quickly transforms design concepts into physical models, accelerating product development and testing.
- Material Diversity: 3D printing has the capability to produce objects using a range of materials such, as plastics, resins, metals, ceramics and more.
- Cost-effective: More economical for small batch production of complex or customized items.
- Digital Manufacturing: Relies on digital files, making storage, transfer, and modification convenient.
3D Printing Technology
The main 3D printing technologies used for Metal Prototyping are SLS (Selective Laser Sintering) and EBM (Electron Beam Melting).

SLS 3D printing
SLS 3D printing fuses metal powders with a laser to create 3D objects. It doesn’t need support structures, so it can make complex shapes.

EBM 3D printing
EBM 3D printing is ideal for making metal parts that need high strength and complex internal structures, like components for aerospace and medical fields.
Sheet Metal Fabrication
Sheet Metal Fabrication is the process of transforming metal sheets into desired parts and products through a series of steps, which typically include cutting, forming (like bending and folding), punching, welding, and Stamping.
Here are some common Sheet Metal Fabrication methods:

Sheet Metal Cutting
Sheet Metal Cutting is the process of dividing metal sheets into the required sizes and shapes. Cutting techniques include laser cutting, plasma cutting, water jet cutting, and traditional shearing.

Sheet Metal Bending
Sheet Metal Bending alters the shape of metal sheets by applying force without changing their volume or thickness. Common bending techniques include brake bending, roll bending, and tube bending.

Sheet Metal Punching
Sheet Metal Punching is the process of creating holes or shapes in metal sheets. It can be done using a turret punch, CNC punch, or hydraulic press and is suitable for manufacturing large quantities of parts with consistent holes and shapes.

Sheet Metal Stamping
Sheet Metal Stamping is the process of using dies and presses to shape metal sheets into specific forms or designs. This technique is crucial for creating parts with complex shapes and is widely used in the automotive and electronics industries.
It’s important to note that a Sheet Metal Prototype typically requires a combination of several Sheet Metal Fabrication techniques. For example, a computer housing may need Sheet Metal Cutting, Sheet Metal Bending, and Sheet Metal Punching technologies.
Metal Casting Prototypes
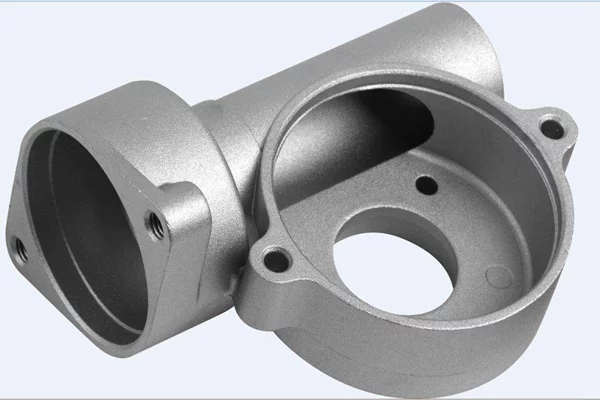
Metal Casting Prototypes are replicas of metal parts made using casting processes. Metal Casting is an ancient technique where molten metal is poured into molds, and the desired shape is formed as it cools and solidifies.
Advantages of Metal Casting Prototypes
- Rapid Iteration: Metal Casting Prototypes allow for a quick transition from design to physical object, which helps to accelerate the product development process.
- Complex Geometries: Metal Casting Prototypes can produce parts with complex internal structures and details.
- Material Diversity: Metal Casting Prototypes can use a variety of metals and alloys, including aluminum, iron, steel, copper, and magnesium alloys, among others.
- Cost-Effectiveness: For mass production, Metal Casting Prototypes are a cost-effective method since molds can be reused.
- Strength and Durability: Parts made from Metal Casting Prototypes typically have excellent mechanical properties and durability.
As technology advances, Metal Casting is also continuously improving. Nowadays, CNC machining is commonly used to manufacture molds for Metal Casting. After the prototype is extracted from the mold, it usually requires further finishing processes such as sanding, polishing, coating, or other surface treatments to enhance appearance or provide protection.
Aluminum Extrusion

Aluminum Extrusion is a manufacturing method where aluminum alloy is pushed through a die with a specific cross-sectional shape to create the required profile.
Advantages of Aluminum Extrusion
- Diversity: Aluminum Extrusion can produce a wide variety of complex shapes and designs, offering high design flexibility.
- High Strength: Despite aluminum’s lower density compared to many other metals, aluminum extrusion products typically have high strength, making them very effective in structural applications.
- Corrosion Resistance: Aluminum naturally forms a dense oxide layer that protects it from further corrosion, so aluminum extrusion parts have excellent corrosion resistance.
- Cost-Effective: Compared to other metals, aluminum is relatively low-cost, and the extrusion process itself is also relatively economical, making aluminum extrusion parts competitive in terms of cost.
- Precise Tolerances: Modern extrusion technology can produce parts with very precise tolerances, which is crucial for engineering applications that require precise fits.
Aluminum extrusion is widely used in industries like construction, automotive, electrical conduits, and many others due to its durability, strength-to-weight ratio, excellent thermal conductivity, stylish appearance, broad application scope, ease of secondary processing, short and cost-effective mold production cycle, and its ability to absorb impacts and deform without breaking.
Common Rapid Metal Prototypes Materials
A variety of metal materials can be used for Rapid Prototyping, each with its unique characteristics, processing methods, and Uses.
Next, I will introduce several metal materials frequently utilized in Rapid Prototyping.
Material | Properties | Processing Methods | Uses |
---|---|---|---|
Aluminum 6061 | Lightweight, good mechanical properties, and weldability | CNC Machining, 3D Printing, Sheet Metal Fabrication, Metal Casting Prototyping | Aerospace, Automotive, Bicycle Frames |
Stainless Steel 304 | Corrosion-resistant, good mechanical properties | CNC Machining, Sheet Metal Fabrication, 3D Printing | Medical Devices, Kitchenware, Chemical Equipment |
Titanium 6Al-4V | High strength, low density, corrosion-resistant | CNC Machining, 3D Printing, Metal Casting Prototyping | Aerospace, Medical Devices, Sports Equipment |
Brass | Good electrical and thermal conductivity, easy to machine | CNC Machining, Sheet Metal Fabrication, Metal Casting Prototyping | Electronic Components, Musical Instruments, Decorative Items |
Copper | Excellent electrical and thermal conductivity | CNC Machining, Metal Casting Prototyping | Electrical Wires, Pipes, Heat Exchangers |
Steel | Good mechanical properties and durability | CNC Machining, 3D Printing, | Structural Components, Automotive Parts, Tools |
Magnesium Alloy | Lightweight, high strength | CNC Machining, 3D Printing, Metal Casting Prototyping | Aerospace, Portable Electronics, Sports Equipment |
Bronze | Corrosion-resistant, easy to machine | CNC Machining, Sheet Metal Fabrication, Metal Casting Prototyping | Marine Engineering, Sculpture, Bearings |
Rapid Metal Prototypes Finishing
Finishing is an Important step in the manufacturing process that enhances the appearance, corrosion resistance, wear resistance, and other properties of the parts.
Below is a table outlining some common methods of metal part finishing and their characteristics:
Finishing Method | Characteristics |
---|---|
Anodizing | Provides corrosion resistance, increases hardness, allows for coloring, suitable for aluminum and titanium alloys. |
Electroplating | Enhances wear resistance, offers a protective coating, can be applied to both metals and non-metals. |
Powder Coating | Durable, chemically stable, suitable for a variety of metals, and emits no volatile organic compounds (VOCs). |
Polishing | Improves surface smoothness, enhances appearance, can be done manually or mechanically. |
Sandblasting | Creates an even rough surface, removes burrs, and can improve the adhesion of coatings. |
Painting | Protects metal from corrosion and offers a range of colors and textures. |
Nickel Plating | Increases hardness, improves electrical conductivity, often used as an underlayer for other platings. |
Chrome Plating | Offers a high gloss, is wear-resistant and corrosion-resistant, commonly used for decorative purposes and to enhance wear resistance. |
Brushing | Provides a unique texture, improves appearance, often used for decorative surfaces. |
Laser Etching | Delivers precise marking that is long-lasting, suitable for a variety of metals. |
These finishing methods can select based on the specific needs and intended use of the metal parts.
For examples, if corrosion resistance is desired, anodizing or passivation treatments can be chosen. If wear resistance is a priority, electroplating or chrome plating might be selected. To enhance appearance, polishing or brushing could be the preferred options. Each method has its unique applications and advantages.
Rapid Metal Prototypes Examples & Cost
The cost of Rapid Metal Prototypes is challenging to estimate without actual requirements, as the evaluation of the price takes into account factors such as the complexity of the prototypes, material, quantity, and precision requirements.
However, we can provide some examples and costs of Rapid Metal Prototypes for your reference.
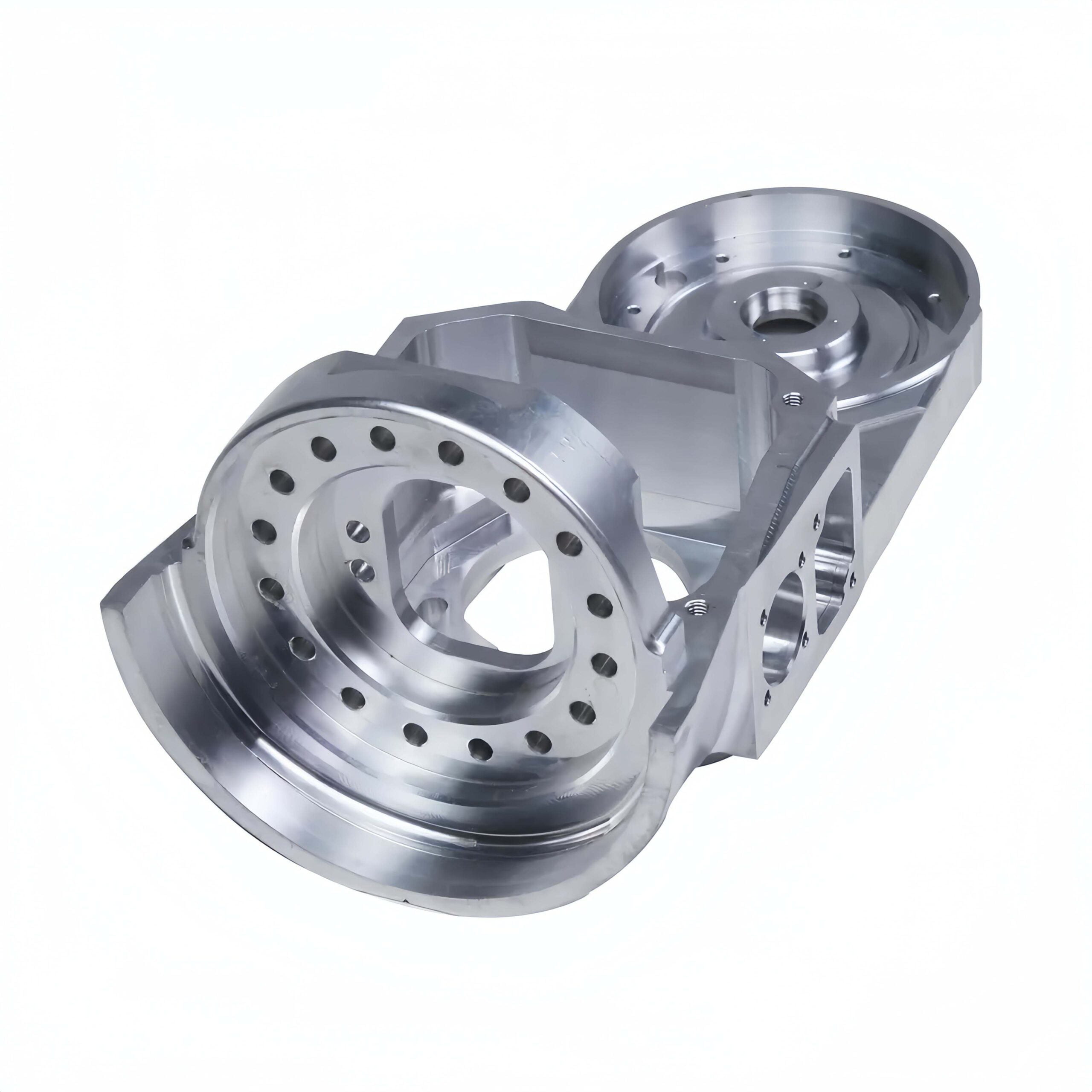
CNC Machining Examples
A CNC metal part made by Aluminum 6061 which cost around $300.
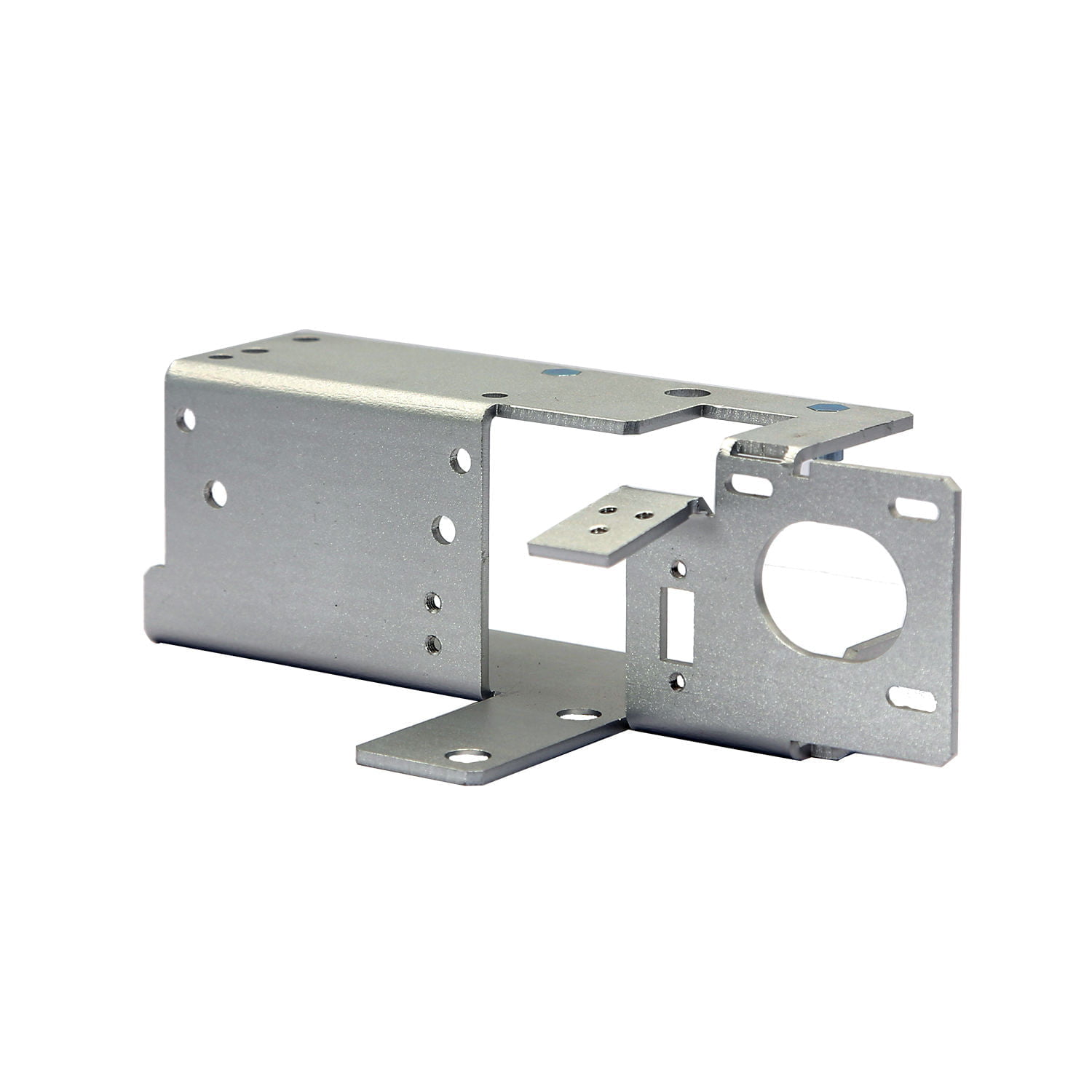
Sheet Metal Examples
this is a sheet metal prototype made by steel which cost around $20.
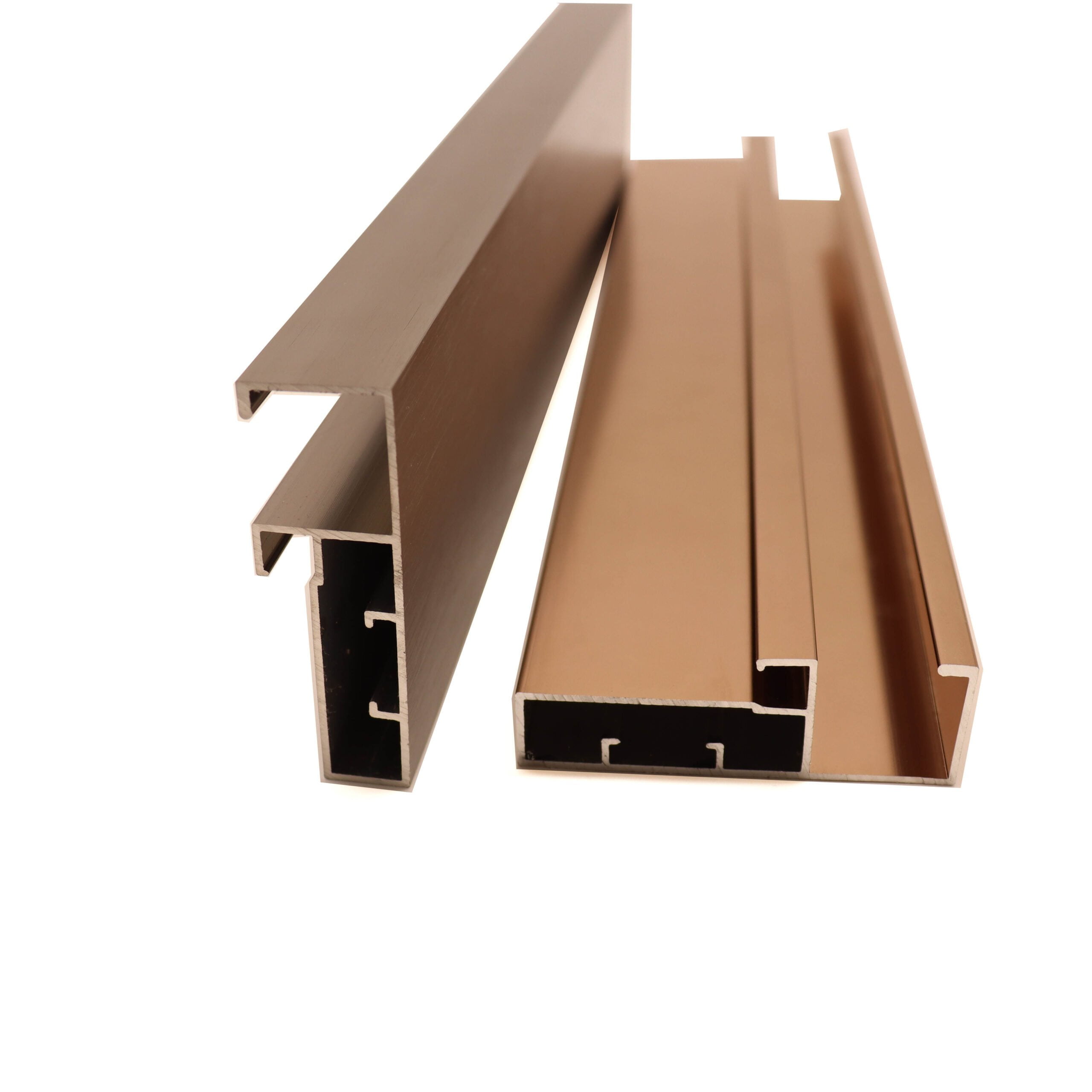
Aluminum Extrusion examples
A aluminnum extrued profile made by aluminum 1100 with Anodizing treatment, cost around $50.
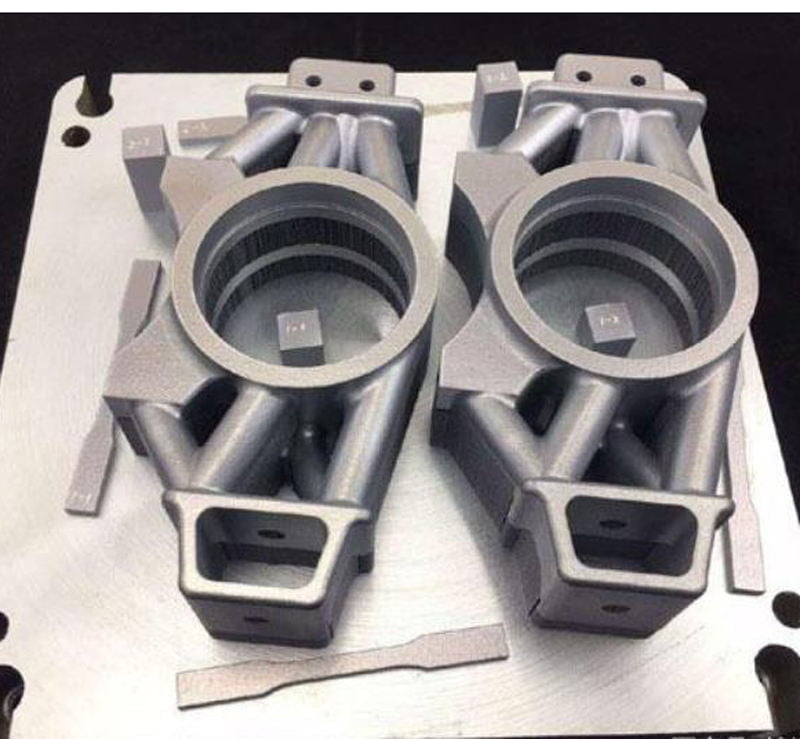
3d Printing examples
a 3D printed aluminum prototype use in automotive industry, which cost around $200.
FAQ About Metal Prototypes
How long does it take to manufacture a Metal Prototype?
On average , from 5 days to 4 weeks. The time it takes to manufacture a Metal Prototype can vary depending on different needs and circumstances. Factors such as the shape, quantity, and manufacturing method of the prototype need to be determined.
Who uses rapid prototyping?
Typically, engineers and designers can create better final products more quickly by utilizing rapid prototyping to produce physical prototypes.
How to get a high-quality Metal Prototype at the lowest possible cost?
This typically relates to the local industry chain, labor costs, and company size of the Rapid Prototyping Company. Kusla, is a Rapid Prototyping Company from China, offers lower prices and higher quality.
In Summary
Using Rapid Metal Prototypes can save you time and money by identifying potential issues early on.
There are various methods to achieve Rapid Metal Prototypes, and an extensive range of metals and alloys available for use. Designers need to select different metals and manufacturing methods based on their understanding of the product.
Equipped with advanced machinery and a team of highly skilled professionals, Kusla specializes in rapid prototyping for both plastic and metal. From high-precision manufacturing to finishing, we can help enhance agility at every stage of your product’s lifecycle. Contact us now for more guidance on your project!