Diamond turning technology, an advanced optical parts processing technique, has been widely promoted and utilized by American research institutions since the 1980s. The products produced using this method feature exceptional surface quality and high precision. As a result, many optical components in modern optical systems depend on diamond turning to achieve ultra-precise, high-quality parts. But how exactly does diamond turning work? In this article, we’ll provide you with a comprehensive guide to this cutting-edge technology.
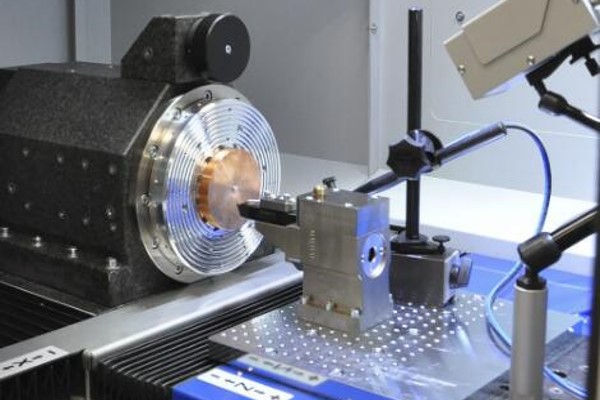
What Is Diamond Turning?
Diamond turning, also known as single-point diamond turning (SPDT), is a high-precision machining process performed on a CNC lathe. In this process, a diamond-tipped cutting tool is used to remove material from the workpiece. The tool’s small radius ensures that only a single point makes contact with the surface of the workpiece, which is where the term “single-point” in single-point diamond turning come from.
How Does a Diamond Turning Tool Work?
Diamond turning utilizes a specialized precision lathe tool equipped with a natural diamond at the cutting tip. Due to the exceptional hardness and sharpness of diamond, these tools can achieve extremely fine cutting precision. The cutting edge of the diamond tool typically has a radius as small as 100 nanometers (nm), with some tools capable of achieving even finer radii of 10-30 nm.
When the diamond tool is applied to the workpiece, it moves at high speed, using the diamond’s sharp edge to grind away material. This process not only shapes the material but also polishes it to a high level of surface smoothness. Unlike traditional metal cutting tools, which rely on the shear strength of the material to remove it, diamond turning is based on the ability of the diamond to microscopically shear and polish the material, resulting in ultra-precise dimensions and a mirror-like finish.
Benefits of Diamond Turning
Compared to other machining processes, diamond turning offers several advantages, especially when producing high-precision parts. Let’s take a look at the key benefits:
High Precision
The most benefit of Diamond turning is that it can achieve ultra-precise dimensions. The surface roughness of parts produced by diamond turning can be as low as 4 nm RMS, ensuring exceptionally smooth finishes and tight tolerances.
Material Versatility
A wide range of materials including metals, plastics, and ceramics can be machined by diamond turning. here are common materials for the diamond turning process:
- Metals: copper, aluminum, nickel, and brass
- plastics: like Acrylic(PMMA), polystyrene (PS), and optical polyester (OKP4).
- Infrared materials like silicon and chalcogenide glass.
Cost-Effective
Diamond turning offers cost-saving benefits, particularly for prototyping in small batches. The process eliminates the need for costly tooling and allows for rapid iteration, making it an efficient option for producing high-quality optical components on a smaller scale.
Efficiency and Speed
Diamond turning is highly efficient, enabling the production of optical components in just weeks. This ability allows manufacturers to reduce lead times, making it a faster alternative to traditional machining methods.
Diamond Turning Machines
To achieve ultra-precision cutting, the key equipment is a single-point diamond ultra-precision lathe. These machines are designed to provide extremely accurate tool positioning, often with an accuracy of up to 100 nanometers. The overall precision of the machine is influenced by several factors, including the stability of the machine bed, the quality of the spindle guide rails, the control system, and other components.
Diamond turning machines range from 2-axis to 5-axis configurations, offering varying levels of flexibility depending on the complexity of the part being produced. A 2-axis machine is suitable for simpler geometries, while a 5-axis diamond turning machine allows manufacturers to create more complex, freeform surfaces that would be difficult or impossible to achieve with a 2-axis setup.
Below is an picture showing the different axes of movement in a 5-axis diamond turning machine, highlighting the added capabilities for precision and versatility in manufacturing optical components.
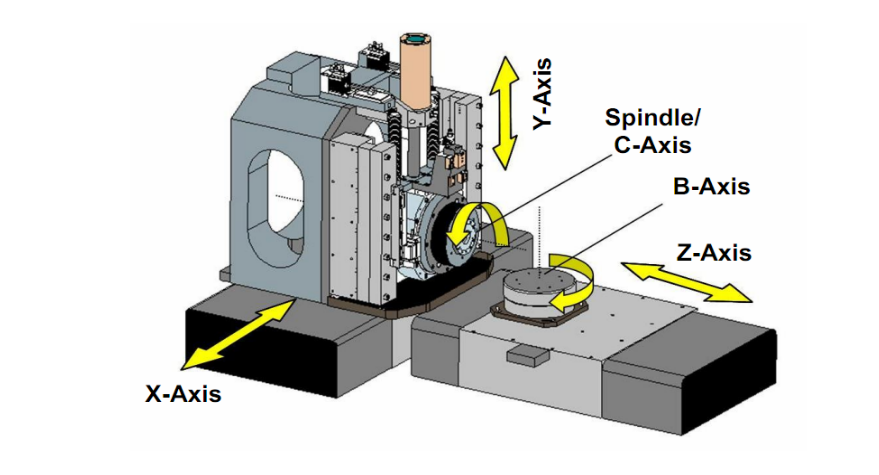
Steps of the Diamond Turning Process
The diamond turning process is similar to traditional turning, but it incorporates a diamond-tipped cutting tool for the final stage of fine precision machining. Here’s an overview of the key steps involved in the diamond turning process:
Step 1: Prepare the CAD model
The first step is to either receive a 2D or 3D CAD model from the client or create the CAD model using CAD software. This model serves as the blueprint for the part to be machined.
Step 2: Programming
Next, use CAM (Computer-Aided Manufacturing) software to convert the CAD model into G-code. The G-code contains the instructions that guide the CNC machine, specifying the cutting path, tool speeds, cutting depths, and other critical parameters.
Step 3: Set up the machine
Before beginning the machining process, securely mount both the diamond cutting tool and the workpiece. A gauge is used to ensure that the workpiece is perfectly centered on the spindle, guaranteeing that the rotation axis aligns with the spindle for maximum accuracy
Step 4: Start rough turning
The machine is then run according to the CNC program to perform the rough turning operation. In this stage, a traditional cutting tool is used to roughly shape the workpiece, leaving a 0.5mm layer for the finer cutting step to follow.
Step 5: Start fine turning
After rough turning is complete, replace the traditional cutting tool with a diamond-tipped tool. The machine continues running the program, and the fine turning process begins, which will achieve the final dimensions and surface finish of the part.
Step 6: Quality check
Once the fine turning process is complete, remove the part from the spindle and conduct a thorough quality check. A standard interferometer is used to measure the surface shape, while an interferometric microscope checks the surface roughness.
If any part of the process does not meet the required specifications, the program may be adjusted, and the process is repeated until all dimensions and surface finishes are within the desired tolerances.
Challenges and Difficulties with the Diamond Turning Process
While diamond turning is a powerful technique, it also has its challenges and limitations.
Material Restrictions
The process works well with softer, non-ferrous materials. However, the types of materials that can be used are limited by the diamond tool’s vulnerability to damage when cutting harder metals and alloys.
Speed and Complexity
Diamond tools and SPDT machines are expensive. Additionally, the need for precise environmental control increases the setup cost and complexity.
Tool Wear
Despite being the hardest known material, diamonds can still wear down, especially when cutting tough materials. To maintain optimal performance, regular tool inspections and replacements may be required.
Tips for Diamond Turning
Based on our experience with diamond turning, here are some helpful tips to optimize the process and ensure the best results:
- 1. Use a cooling liquid to cool the contact point when cutting metal. if cutting plastic, then use air to avoid damage to the plastic part.
- 2. Control the room temperature at 20°C±0.5°C, and control the part temperature at 20°C±0.05°C by spraying constant temperature liquid.
- 3. Make sure the diamond turning machine is far from vibration and noise effects which could lead to a bad result.
- 4. Make sure the working room achieves at least the 10000 level of cleanliness to reduce the dust effect.
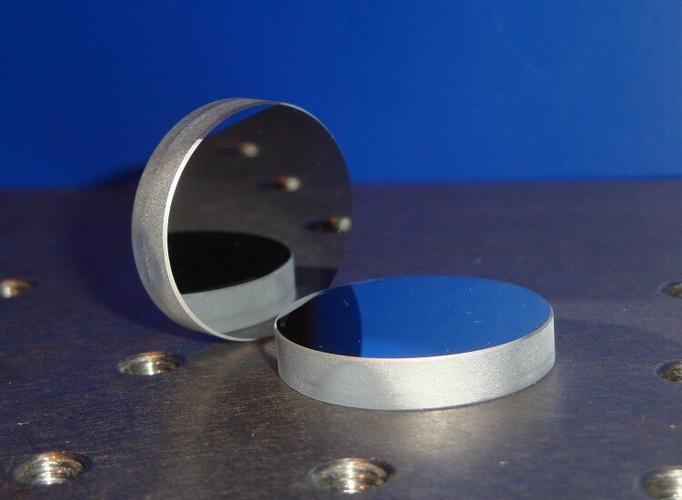
Types of Diamond Turning
Diamond turning offers different methods depending on the desired outcome and the type of part being produced. These methods include traditional turning, off-axis turning, fly-cutting, and freeform machining. Let’s explore each of these in more detail:
Traditional turning
In traditional diamond turning, the process is similar to conventional turning but with a key difference: it uses a diamond-tipped cutting tool to achieve ultra-precise machining. This method is used to produce rotationally symmetric parts, such as lenses and mirrors, but with much higher accuracy and smoother surface finishes than regular turning.
Off-axis turning
Off-axis turning is a technique where the workpiece is mounted asymmetrically to the spindle. In this method, diamond turning can be performed on parts whose rotational center does not align with the center of the workpiece. This is particularly useful for creating optical components where the optical axis and the physical center of the part need to be offset, such as in certain types of lenses or mirrors with specific geometries.
Fly-cutting
Fly-cutting is a method used when a diamond turning lathe allows for reversing the positions of the workpiece and the tool. In this setup, the cutting tool is mounted on the spindle, and the workpiece is mounted on the slide. This technique is commonly used for machining flat or elliptical surfaces, providing a smooth finish with high precision. Fly-cutting is often used to achieve the final surface geometry of optical components like flats or circular optics.
Freeform machining
Freeform machining is a more advanced diamond turning technique that enables the production of complex, non-symmetrical, and freeform surfaces. Using multi-axis CNC machines, freeform machining can create surfaces that are not constrained to traditional geometric shapes, allowing for greater flexibility in optical component design.
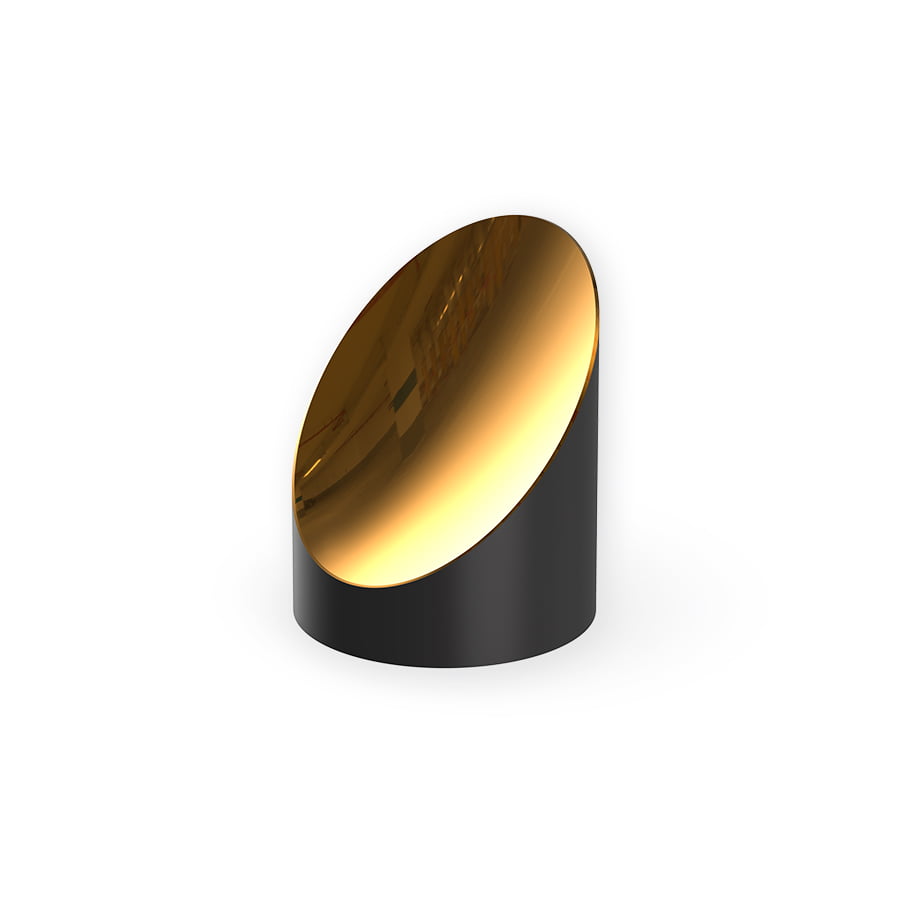
Applications of Single-Point Diamond Turning
After understanding the process and benefits of single-point diamond turning, here are some key applications where this technology is widely used:
Infrared optical aspherical mirror
Diamond turning is ideal for the mass production of aspherical mirrors used in infrared optical systems. These mirrors are often made from materials like germanium, zinc sulfide, zinc selenide, lithium fluoride, barium fluoride, and calcium fluoride. Using diamond turning, manufacturers can achieve exceptional surface shape accuracy (less than 0.2 µm) and surface roughness as low as 0.02 µm, making it suitable for high-performance infrared optics.
Optical lens mold core
Diamond turning is also widely used to create aspherical metal molds and die cores, which are essential for the mass production of optical aspherical lenses. These molds are used in various applications, including the production of lenses for digital cameras, where precise shape and high surface quality are critical for optimal optical performance.
Off-axis aspherical mirror
Off-axis aspherical mirrors are optical components where the optical axis and the mechanical axis do not coincide. These types of mirrors are crucial in systems where the optical path needs to be offset, such as in certain types of telescopes and imaging systems. Diamond turning allows for the precise production of these off-axis aspherical mirrors, providing high accuracy and performance.
Freeform mirror
Diamond turning is also used to produce freeform mirrors, which have complex, non-symmetrical shapes that are difficult to achieve with traditional methods. These mirrors, made from materials like copper and aluminum, are increasingly used in imaging systems, displays, laser coupling, and other photoelectric applications. Freeform mirrors enable more flexible design possibilities in advanced optical systems, particularly in applications where space or weight constraints are critical.
Conclusion:
This guide has provided a comprehensive overview of diamond turning, helping you understand why it is widely used for producing optical mirrors and other precision optical components. At Kusla, as a trusted diamond turning service provider, we specialize in custom nanoscale optical parts, including flat, spherical, aspheric, freeform, and other core optical components. If you have any questions about the diamond turning process or need customized optical parts, please don’t hesitate to contact us. We’re here to assist with all your precision machining needs!
FAQ
Can diamond turning work on Polycarbonate material?
Yes, diamond turning can be applied to polycarbonate, but it is generally not the best choice. Polycarbonate is a relatively soft material, and during the cutting process, it tends to produce burrs that can affect the surface quality. These burrs usually require a secondary polishing process to achieve the desired finish.
Does diamond turning need a secondary polishing process?
No, diamond turning does not typically require a secondary polishing process. One of the main advantages of diamond turning is its ability to produce a mirror-like surface finish with a surface roughness level of less than 10nm. This high precision is achieved directly during the turning process, eliminating the need for additional polishing in most cases.