
Injection molding is a widely used process for manufacturing plastic parts, but it requires significant investments in steel molds and injection machines. When only small batches of parts are needed, traditional injection molding often becomes cost-ineffective. In such cases, low-volume injection molding offers a more economical solution. This article provides a guide to this process, helping you understand what it is and how it works. Let’s dive in!
What is low volume injection molding?
Low-volume injection molding is a process used to produce small batches of plastic parts, typically ranging from 100 to 10,000 pieces. It is ideal for creating prototypes, small-scale productions, or custom parts used in various applications.
This process uses simpler, smaller molds and compact machines that require less force and cost less to set up compared to traditional injection molding. It is a more affordable and efficient option for producing high-quality parts in small quantities.
key Benefits Of Low-Volume Injection Molding
Low-volume injection molding offers many advantages, especially in terms of cost, speed, and flexibility. let us explain these benefits in details:
Bridge to Mass Production
Low-volume injection molding is an excellent way to transition from prototypes to mass production. It allows companies to test and refine both the product and the manufacturing process without committing to full-scale production, effectively bridging the gap between prototyping and production.
Cost efficiency
For small production runs, low-volume injection molding significantly reduces costs. this is because It uses less expensive mold materials, like aluminum or soft steel, and avoids the high upfront costs of traditional tooling.
Faster lead time
The process involves using rapid molds, which are quicker and easier to produce than traditional steel molds. Rapid tooling can reduce mold-making time from months to just weeks. With molds ready faster and smaller production volumes, the entire process moves quickly, helping companies bring products to market sooner.
Easy Design Changes
This method is ideal for custom or evolving designs. It’s easy to make adjustments between production runs, and the molds can be modified at a low cost. This flexibility allows for quick corrections and improvements before committing to large-scale production.
High-Quality
Low-volume injection molding ensures excellent surface finishes, reducing the need for extra polishing or post-production work compared to other rapid prototyping methods, such as 3D printing. This is especially important for products where appearance matters, like consumer goods and visible parts.
Use of Low volume injection molding
Low-volume injection molding is a cost-effective manufacturing solution commonly used for rapid prototyping, short-run injection molding, and on-demand or custom injection molding. Let’s explore these common uses in more detail:
On demand manufacturing
On-demand manufacturing allows businesses to produce parts as needed, reducing the need for large inventories and lowering storage costs. This flexibility makes it easier to adapt to fluctuations in demand, making low-volume injection molding an ideal choice for businesses in unpredictable industries, helping reduce risks and improve efficiency.
Rapid Prototyping
When making plastic prototypes, Low volume injection molding can be used a prototype inejction molding to create prototypes in just few pieces. The key benefit of this method is that it uses rapid tooling, enabling prototypes to be made from production-grade materials. This provides more accurate test results, closely reflecting the final production design.
Small production runs
As the name suggests, low-volume injection molding is perfect for creating small batches of parts. This way provides an economical solution for businesses that may not have the capital for large-scale production. It allows businesses to produce parts in small quantities and respond quickly to changing market demands.
How Low-Volume Plastic Injection Molding Works
Low-volume injection molding follows a series of steps similar to high-volume molding but uses smaller equipment and machines. Let’s walk through each step to understand how it works:
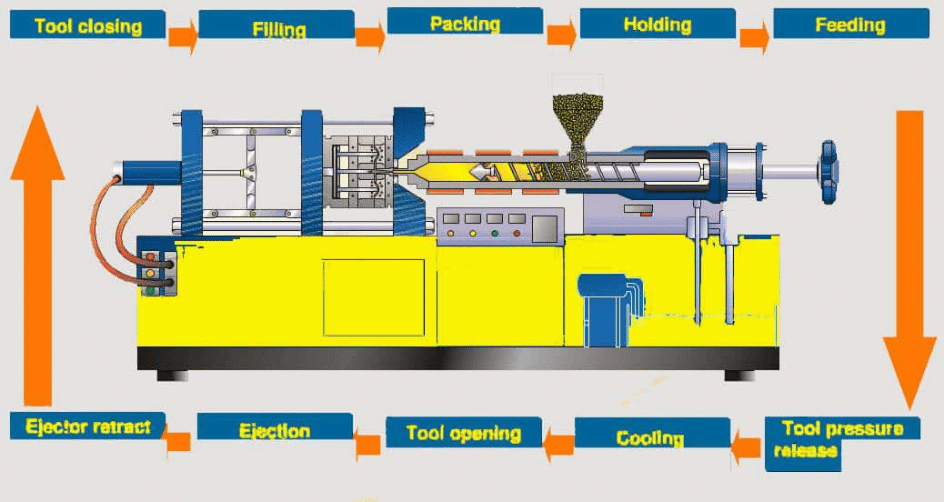
1. Tooling Mold Design
The process begins with designing the mold. Engineers identify the specifications of the final plastic part, including its shape, size, and material. Using CAD software, a detailed 3D model of the mold is created. For low-volume production, aluminum or soft steel is commonly used for the mold due to their cost-effectiveness and ease of machining.
2. Molding Making
After the mold design is finalized, the next step is manufacturing the mold itself. This can be done through CNC machining or 3D printing, depending on the complexity and requirements of the mold. CNC machining is commonly used to create precise and durable molds from materials like aluminum or soft steel, ensuring high accuracy and long-term reliability. For simpler mold designs, 3D printing is a faster and more cost-effective option, allowing for quicker turnaround times.
3. Mold clamping
Once the actual mold is ready. Clamp the mold on the injection machine. A clamping system securely holds the mold in place, ensuring the two halves are tightly closed. The clamping force must match the injection pressure to prevent any gaps or movement during the process. Components such as ejector pins are also installed at this stage to assist with part removal later.
4. Setting Up the Injection Machine
In this step, The Technicial will configure the injection machine by setting parameters like temperature, pressure, and injection speed. A test run is conducted to fine-tune the settings and ensure the process produces high-quality parts.
5. injection
During this phase, the plastic material is melted and transferred to the injection barrel. The molten plastic is then injected into the mold cavity under high pressure, filling the design shape completely. The specific process may vary based on the type of machine being used.
6. Cooling
After the mold is filled, the plastic cools and solidifies inside the cavity. Cooling time depends on the type of plastic and the material of the mold. Aluminum molds cool faster than steel, but cooling can be further accelerated with compressed air or interchangeable cooling stacks. Proper cooling ensures the part retains its shape and dimensional accuracy.
7. Demolding
Once the part is fully cooled, then, it is removed from the mold. This can be done manually or automatically using ejector pins. A release agent may be applied for thermoplastics with high viscosity to facilitate smoother removal.
8.Post-Processing
After demolding, some parts may require additional processing. For instance, excess material, known as “flash,” can escape along the mold’s parting line and needs to be trimmed or removed.
Rapid Toolings for Low-volume Injection Molding
Three common types of rapid tooling are widely used in the low-volume injection molding process: 3D printing polymer tooling, aluminum tooling, and soft steel tooling. The choice of tooling depends on the specific needs of the project. let us explore the details of these rapid toolings:
Polymer Tooling by 3D printing
3D printing is used to create the plastic cavity and core of the tooling using high-temperature-resistant plastic materials. This method allows for extremely fast production of tooling, making it ideal for projects that require a short lead time. It is particularly suitable for low-volume production runs involving plastics with low melting points.
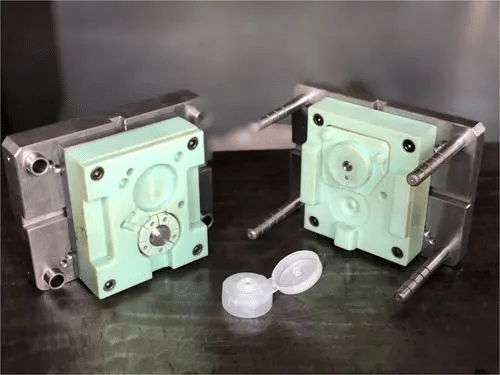
Aluminum Tooling
Aluminum Tooling is another good choice for low-volume injection molding because Aluminum is an easy machinable metal by CNC machining, which can save time in manufacturing the tooling. Aluminum tooling usually produces plats parts of less than 1000 pieces because aluminum is not so strong enough to resist the impact of too many times injections.
Soft Steel tooling
Soft steel Tooling does not mean the steel used for mold is soft. this only compares with the hard tooling used for mass production. Two primary types of soft steel tooling used for low-volume injection molding are P20 and NAK80. Soft steel is harder than aluminum which has a better lifespan which means it can used for producing more parts and up to 10000 pieces.
A Comparison table of the three methods above is below, you will see which one is suitable for your project
3D printed polymer | aluminum tooling | Soft steel Tooling | |
Tooling cost | <$100 | $200 – $1,000 | $500 – $4,000 |
Lead time to final parts | 1-3 days | 2-3 weeks | 3-4 weeks |
Ideal production volume | <500 | 500 – 1,000 | 1,000-10,000 |
Low-volume injection molding materials
The plastic materials used in low-volume injection molding are the same as those used in high-volume production. Common materials include PMMA, PC, ABS, PP, POM, Nylon, and others. Below are the most common plastics used in low-volume plastic injection molding:
- acrylic (PMMA)
- acrylonitrile butadiene styrene (ABS)
- nylon polyamide (PA)
- polycarbonate (PC)
- polyethylene (PE)
- polyoxymethylene (POM)
- polypropylene (PP)
Injection Molding Design Considerations
There are some key design considerations that you must keep in mind for effective low volume injection molding process to make high quality parts. Let’s go through these key considerations in detail:
Material
The first step for low-volume injection molding is to choose the materials for your product. this is because the material you use for injection molding will affect the materials of the tooling you can use. high melting point materials require high strength and high-temperature resistance tooling materials such as Aluminum and Steel. so, you need to evaluate the functions of your product and choose those materials easy to inject.
Part’s Finish
Check the level of the part’s finish, as it is related to the precision of the tooling surface and can increase the cost to achieve it. A common mistake in plastic injection molding is requesting a surface finish that is smoother than necessary, which can add complexity and impact the part’s functionality. If a smoother finish is required, consider using hand polishing to achieve the desired result.
Draft
Even with rapid tooling, it’s important to include draft angles in your design, when possible. These slight angles on the sides of the part make it easier to remove from the mold and reduce issues during injection molding.
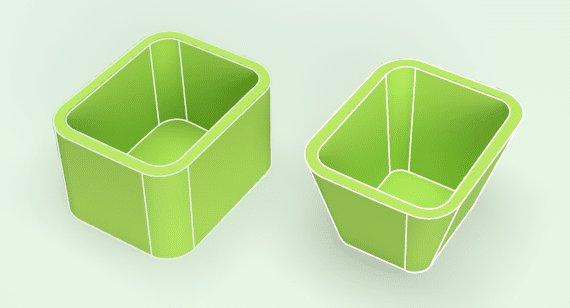
Wall Thickness
Wall thickness is a critical factor in plastic parts production. To avoid shrinkage or warping during the molding process, the wall thickness should be consistent and follow industry standards. Typically, the recommended thickness for plastic parts is between 1.5mm and 3mm.
Radii
Rapid toolings are often machined using end mills, which may not work well for sharp internal corners. Adding radii (rounded corners) to your design improves part strength and makes tooling easier to create.
Low-Volume VS High-Volume Plastic Injection Molding
Understanding the differences between low-volume and high-volume injection molding is essential when deciding which method to choose for your project. Let’s compare these two processes based on key factors:
Tooling materials
Low-volume injection molding uses rapid tooling, also known as soft tooling, made from aluminum or soft steel. In contrast, high-volume injection molding uses hard steel to create the tooling, which is more durable and suited for mass production.
lifespan
Low-volume injection molding is suitable for producing fewer than 10,000 parts, while high-volume injection molding is designed for much larger runs, typically producing over 100,000 parts.
Precision
Due to the use of hard steel tooling and a more robust tooling structure, high-volume injection molding can achieve better precision and tighter tolerances in parts compared to low-volume injection molding.
Lead Time for Tooling
The tooling for low-volume injection molding can be created in just 2-4 weeks, whereas high-volume injection molding tooling takes much longer—typically 12 to 16 weeks. This shorter lead time allows low-volume injection molding to get parts to market much faster than high-volume methods.
Cycle Time of Parts Injection
High-volume injection molding benefits from greater automation, allowing for quicker injection cycles and lower part costs due to the ability to produce parts at a faster rate. Low-volume injection molding, on the other hand, has longer cycle times and is more suitable for small production runs.
Partner with Kusla’s low-volume Injection molding service
When choosing a company for low-volume injection molding, it’s important to select one that has the right expertise. Picking the right company leads to better results for your project. The company should understand your needs and apply the best methods to achieve them. This way, you’ll get the final product you want, without any issues or unexpected costs. KUSLA prototype specializes in low-volume injection molding for businesses in various industries to help turn your ideas into a reality.
FAQ
What is the minimum quantity for Low-Volume Injection Molding?
The minimum quantity is only one piece for rapid prototyping. and 1,000 pieces for a short-run production.
How much does low-volume injection molding Cost?
On average, the low-volume injection molding cost for small and simple parts is around $500 – $10,000 in total including tooling cost and injection molded part cost.