Ultra-precision machining is very important for many industries like aerospace, medical, automotive, and electronics. It helps make very detailed and accurate parts that improve how things work, last longer, and use energy more efficiently. This type of machining is often needed in fields that require extremely high accuracy, such as making airplane parts, surgical tools, and precision tools. In this article, we explain what ultra-precision machining is and describe common methods used to create parts with very tight tolerances and smooth surfaces. Here we go!
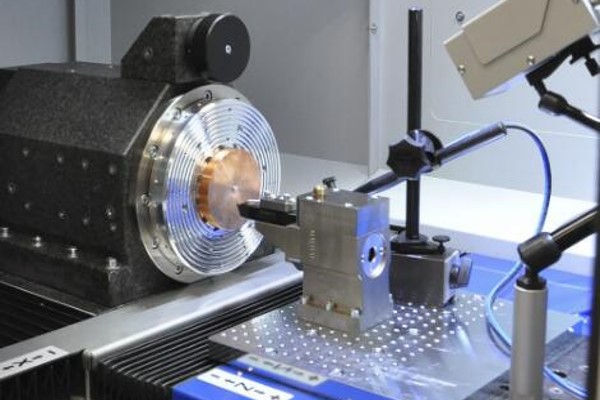
What is Ultra-Precision Machining?
Ultra-precision machining is an advanced manufacturing process used to create highly detailed and accurate components with extremely tight tolerances, often as small as sub-micron levels. It involves the use of specialized machinery, advanced tools, and precise control systems to produce parts with minimal tolerances.
Unlike traditional machining, ultra-precision machining can handle challenging materials that are difficult to cut, while maintaining tight tolerances and excellent surface quality. It’s commonly used in industries like aerospace, medical devices, and precision instruments, where the smallest imperfections can impact performance and safety.
Accuracy of ultra-precision machining
Before diving deeper, let’s first discuss machining accuracy. The accuracy of ultra-precision machining can be categorized into different grades, depending on the specific requirements and applications. These grades typically range from the micron level to the nanometer level. Here’s a closer look at the details:
Micron-Level Accuracy
Micron-level accuracy refers to the ability to achieve very precise size, shape, and surface quality in machining, with measurements reaching the micron (μm) scale. The accuracy typically ranges from 3μm to 0.3μm, while surface roughness falls between 0.3μm and 0.03μm. This level of precision is often used in high-precision tooling and applications where fine detail is required.
Nanometer-Level Accuracy
Nanometer-level accuracy is even more precise, typically around 30nm, with surface roughness reaching less than 5nm. This level of precision is essential in fields like ultra-precision optical components, nanotechnology equipment, integrated circuits, and other advanced technologies that demand extremely fine detail.
How does Ultra Precision Machining Work?
To achieve ultra-precision, it’s important to understand that every step of the machining process matters. From the machines and tools to quality control, each factor plays a crucial role in ensuring the final product meets the required standards. Let’s take a closer look at how these key factors contribute:
Advanced Machines
Ultra-precision machining relies on high-precision machines such as CNC centers which offer exceptional accuracy and repeatability. these machines are usually controlled by a precision control system and a low thermal expansion system to enhance dimensional stability.
High-Precision Cutting Tools
No matter laser cutting or CNC cutting tools, To achieve ultra-precision machining, the cutting tools need to achieve ultra-precision and stability before starting the machining. High-precision CNC cutting tools are made from materials such as polycrystalline diamond (PCD) and cubic boron nitride (CBN) which can provide high wear resistance and maintain their sharpness, allowing for precise cuts.
Quality Control
Ensuring accuracy in ultra-precision machining requires advanced Quality Control equipment and techniques. Equipment such as laser interferometers and non-contact surface measurement systems ensure parts meet strict specifications and tolerances.
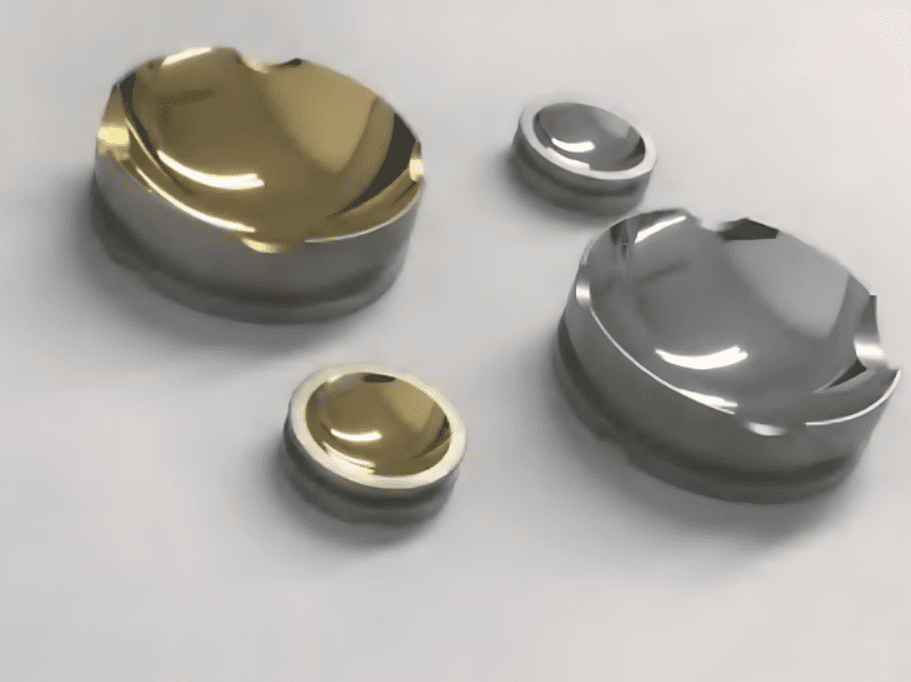
Common Types of Ultra Precision Machining processes
There are several techniques that can achieve ultra-precision machining. Here are some of the most common types:
Diamond turning
Diamond turning also referred to as single-point diamond turning(SPDT), is a high-precision turning process performed on a CNC lathe, Using a diamond-tipped cutting tool to remove the material from Workpieces. the accuracy of Ultra-precision turning can generally reach 10-100nm. it is widely used in optical devices and optical lens manufacturing, high-precision bearings, gyroscope parts, etc.
Ultra-precision grinding
Ultra-precision grinding is a machining process that uses superabrasive grinding wheels as the main tool, performing ultra-micro cuts on ultra-precision machines to achieve extremely high surface accuracy. This technique can achieve accuracies as fine as 0.1μm, with surface roughness as low as 0.025μm. Ultra-precision grinding is mainly used for producing highly accurate parts, such as optical aspheric surfaces, semiconductor silicon wafers, super-hard precision molds, missile fairings, and components like hemispheric resonant gyroscopes.
Wire EDM (Electric discharge machining)
Electric discharge machining is a non-contact metal machining process. It uses electric sparks generated from a high-energy pulse current on the surface of the workpiece to remove the materials of the workpiece. It is especially suitable for machining metal conductive materials with high hardness, complex shapes, and high precision requirements and is widely used in tooling-making industries. Wire EDM can achieve an accuracy level of 0.001mm.
Micro-Precision Laser Machining
Laser machining uses a focused high-energy laser beam to locally irradiate materials to generate high temperatures, which can melt, vaporize, or cause physical and chemical changes in the material, thereby achieving cutting, welding, and drilling. The precision of laser machining can reach the micron level.
Ion beam machining
Ion beam machining uses high-energy ion beams to target the surface of a workpiece at the nanometer scale, causing sputtering (removal of material) and deposition. This process allows for extremely fine material removal with high precision. Ion beam machining is widely used in semiconductor manufacturing, particularly for creating nanopores, repairing integrated circuits, and other applications that require highly detailed work at the micro and nanometer levels.
Chemical polishing
Chemical polishing combines chemical etching and mechanical grinding to smooth the surface of a workpiece. It uses a polishing pad soaked in a chemical solution, applying a specific pressure and speed to achieve a micron-level smooth surface. This technique is primarily used in the semiconductor manufacturing industry to improve the surface finish of components and enhance their performance.
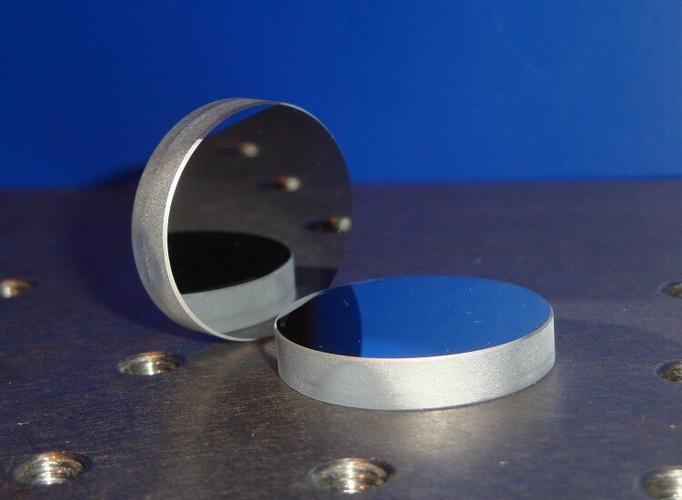
Applications of Ultra Precision Machining
Here, we’ll introduce some of the key applications of ultra-precision machining to help you better understand its importance. Let’s take a look:
Aerospace
In the aerospace industry, ultra-precision machining is used to create critical parts for aircraft and rockets, such as turbine blades and compressor disks, which require extremely high accuracy and reliability.
Biomedical
Ultra-precision machining is crucial in the biomedical sector for manufacturing medical implants such as artificial joints, dental implants, and surgical instruments. These parts must be highly accurate and biocompatible to ensure proper fit, function, and long-term reliability within the human body.
Instruments
Instruments used for scientific research and measurement require ultra-precision machining to ensure exact accuracy. This technology is used to create high-precision measuring instruments, sensors, and scientific equipment that are essential in fields like physics, chemistry, and engineering.
Optical Components
Ultra-precision machining is widely used in the production of optical components, including lenses, mirrors, and optical instruments. These parts must meet strict precision standards to ensure proper light transmission and image clarity in applications such as cameras, microscopes, and laser systems.
Automotive
In the automotive industry, ultra-precision machining helps create critical components, such as engine parts and transmissions, which require exceptional accuracy to ensure performance and durability.
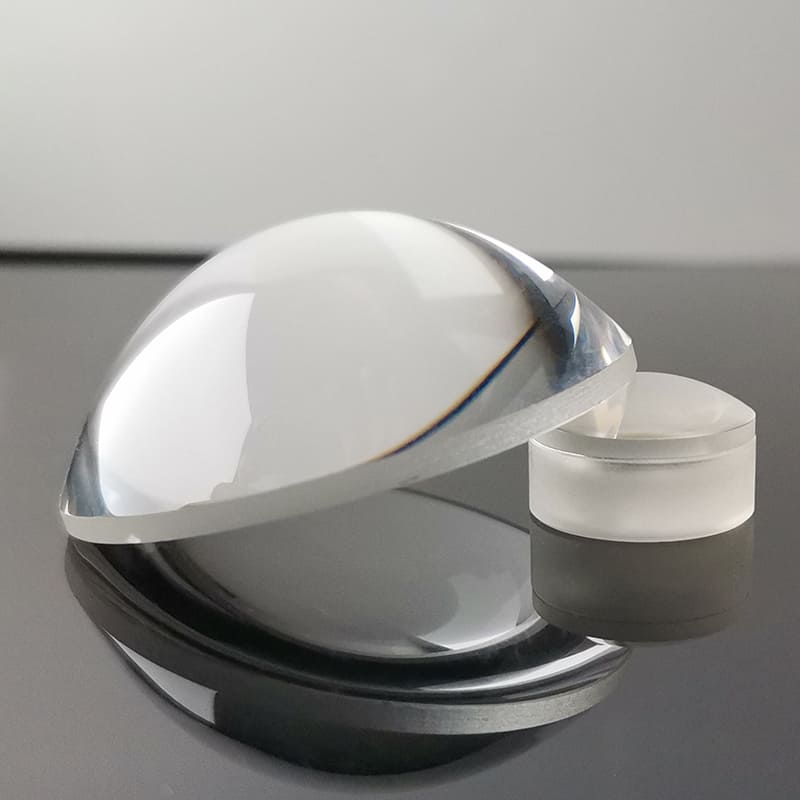
Conclusion
Ultra-precision machining can produce complex parts with outstanding accuracy and high-quality surface finishes, ensuring excellent performance, reliability, and long-lasting results. Achieving this level of precision requires a deep understanding of the machinery, processes, and materials used. KUSLA, a trusted leader in providing diamond turning services, offers advanced equipment and a team of skilled engineers ready to help you meet your most demanding precision requirements..
FAQ
What is the difference between Ultra-precision machining vs traditional machining
The main difference is the level of accuracy they can achieve. Ultra-precision machining can reach extremely tight tolerances and smooth surfaces as small as the nanometer level, making it perfect for industries that need high precision, like aerospace, medical, and optics. On the other hand, traditional machining usually has wider tolerances and is better for less complex jobs. While traditional machining works well for general manufacturing, ultra-precision machining is the best choice for creating detailed and accurate parts where precision is crucial.
Which machining method has higher accuracy and surface finish?
Generally, diamond turning provides higher accuracy than other methods, offering exceptional precision and surface finishes with smoothness as fine as 0.01 μm Ra (average surface roughness). This makes it the preferred choice for producing parts that require extremely tight tolerances, which traditional CNC milling machines may not be able to achieve. Diamond turning is especially ideal for applications where ultra-smooth surfaces and high precision are critical, such as in optics and precision instruments.